Aircraft owners are dependent on their maintenance provider for regular servicing, inspections and evaluating their findings especially when it comes to engine operation and reliability. The maintenance provider is often integral to the decision-making process to determine engine longevity and many of the incidental details associated with overhaul or upgrade. It is expected that an airworthy aircraft will continue to run in accordance with the published operating parameters so there remains an underlying trust that the signing AME will offer the best information on the subject. The pilot must also pay attention to panel indications that may point to more subtle operational concerns and report these observations to their maintenance provider. The AME is then be counted upon for performing good visual inspections, recording findings and testing data, and interpreting engine cylinder compression results as a long accepted indicator of engine health. The AME can also contribute to other discussion points such as effective fuel management, oil analysis and consumption, and looking into other considerations at the request of the owner/operator.
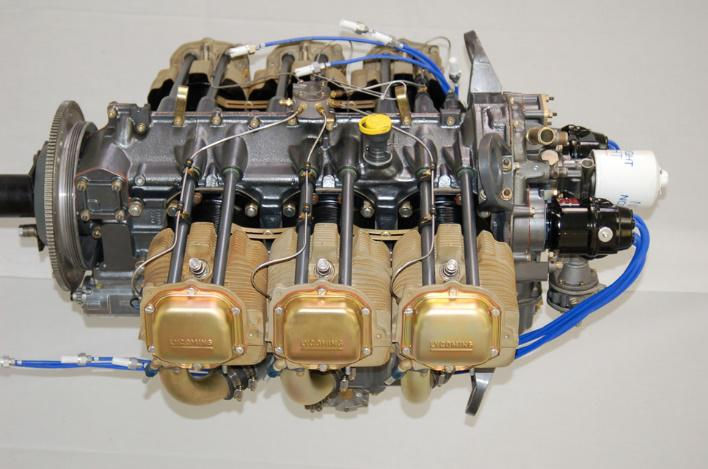
At some point in time, the aircraft ownership experience may present some big decisions such as engine overhaul or upgrade replacement. These decisions take time to formulate and require thinking through the entire process in order to justify the up-front cost and long term value of this type of commitment. We know that engine time-in-service and ongoing serviceability is a key factor towards the ultimate satisfaction of aircraft ownership. For those who have either dealt with an engine change or may be dealing with it in the future, it may be helpful to understand some of the technical details often considered during this critical maintenance centered activity.
Engine conditions leading up to consideration for overhaul or replacement may include failing cylinder compressions, an increase in engine wear metals evident in oil screen or filter, or even a noticeable loss of power output. Depending on the engine time-in-service, failing cylinders may be considered for top overhaul if all other bottom end components remain solid. The engine may have simply reached its published TBO (Time between Overhauls) indicating that it’s time to take action ahead of any tangible signs of deterioration or on-condition considerations. The recommended TBO is published by the engine manufacturer as a pre-speculated target time based on engine model and service severity. Once it has been determined that major overhaul is imminent then the next step becomes engine removal.

Other more immediate causes for engine removal may include sudden engine stoppage such as from a propeller strike, or other types of occurrences such as internal damage or oil starvation. These are primary examples where an engine must be removed for one reason or another for specialized maintenance with the most common being major overhaul/exchange. Either way, these mechanical workhorses aren’t designed to last forever but they are very capable of providing many hours of continued service when diligently operated and maintained. Engine care is ultimately in the hands of both the operator and the maintainer when consciously sharing data and ideas. The critical process of engine removal should also involve looking at the engine mount, accessories and associated wiring. The engine baffles, seals and air intake structure will also demand attention now that everything is becoming easily accessible. There is actually much more to consider besides freeing the engine of its connections, attaching it up to a hoist and hauling it out with reckless abandon.
More complex installations require us to consider taking some strategic photographs of the engine configuration and specifically the routing of hoses, wire bundles and engine controls. Sometimes it just looks as though there is no real order to it all when there actually may be a good reason for the existing routing. On the other hand, it may become necessary to correct a previous installation that was inadvertently set up for premature wear or stress. The time taken to ensure a good overview of the installation before disconnecting these items will often pay off when the time comes to put it all back together again. Previous experience and a good memory do help but having pictures on file will tell the story for anyone returning to or taking over the job of re-installation. Labelling items with masking tape and making detailed notes are two proven methods of identifying proper orientation or other specific details before disassembly. The aircraft service manual also provides a guaranteed reference for certain details that we may have only encountered through hands-on training.
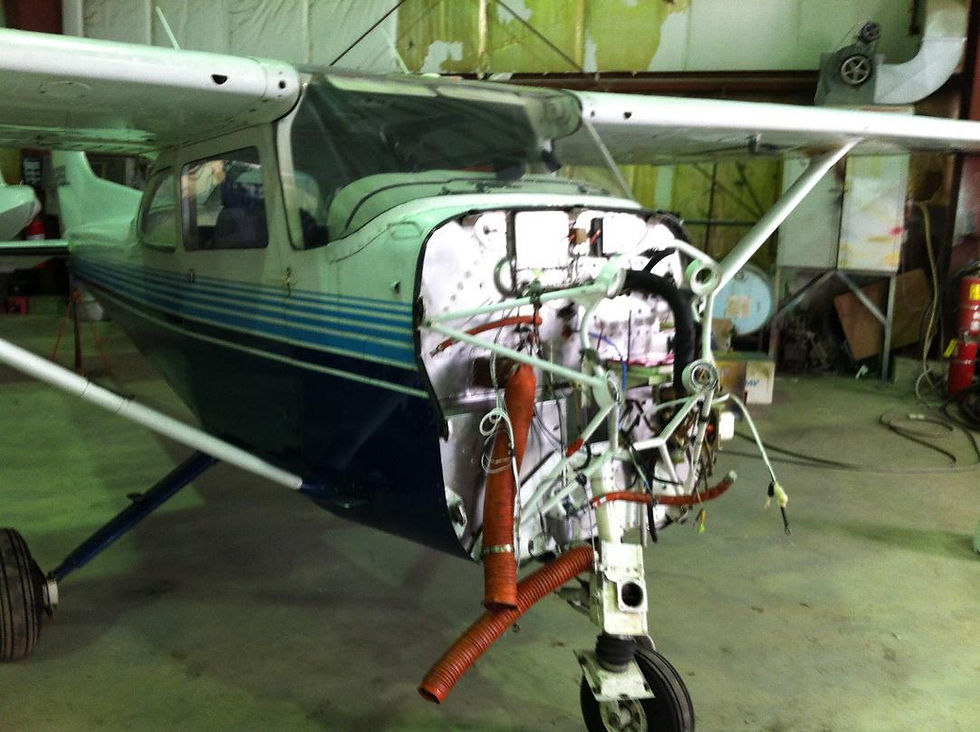
If the flexible fuel and oil hoses are to be re-used, they can remain attached to their firewall fittings with the open end properly capped to prevent contamination during the flow of work. In some cases, these hoses should really be flushed out to ensure that any metal or dirt contamination has been fully eliminated from the system. Depending upon the nature of the installation and specific routing, engine compartment hoses have the necessary heat protection in the form of orange fire sleeve material or strategically placed heat shields and stand-offs. It makes good sense to also consider the condition of these items at this time. Even though flexible hoses have a pre-determined service life, they must also be inspected for condition resulting from chafing, bending, and excessive heat exposure. This isn’t the time to make-do with spending less on the overall job. If a hose is of questionable condition, then replace it. A failed hose in flight can quickly put a stop to things going round and round. Thorough servicing and/or replacement of all items relating to the engine provides an ideal starting point since the engine has just had major work done.
Engine components like the alternator, vacuum pump or oil cooler should be inspected for service history and condition at this time. Perhaps it is also time to consider overhaul/exchange to coincide with the engine work. The muffler should also be carefully inspected around all of the welded joints and attachments. Check over the engine cowling for condition of the air intake scoop and/or air box and cowl flaps for proper operation. Undetected flaws in the air inlet system (including the air filter element itself) may permit contamination to your newly installed engine. Engine cooling or heating SCAT hoses should be inspected for deterioration and replaced as necessary for the same reason. They are vulnerable to punctures, tears and even oil soaking after extended hours in service. Brittle wiring, clamps and tie wraps should be inspected and replaced as necessary while access to tight areas along the firewall has never been better. All of these considerations mentioned above are merely the extras that are worth looking into outside of the primary task of replacing the engine.

Once the all-important tail stand (for tricycle configured aircraft) has been attached before releasing the engine from its mount, the aircraft will remain where it sits until mobile again with the necessary weight up front again. With the propeller removed to facilitate engine removal, it could also be inspected at this time especially in the hub area. Constant-speed propeller models having been subject to wear metal contamination must be flushed out anyways and inspected before re-installing. Prop installations which have been weighted for dynamic balance ought to be re-balanced following re-installation of the engine/propeller.
As with any routine inspection, the many incidental items removed from the outgoing engine should all be cleaned and set aside to an area of the shop designated to keep these items organized. Make note of any special fittings and their orientation on the engine to ensure proper positioning. Take note of any parts to be replaced, including gaskets and hardware, while the engine is out while planning ahead for the subsequent re-installation. The projected aircraft down time may even be a good opportunity to consider other jobs that need performed on the airframe if it can be arranged. Any major overhaul, exchange or cylinder re-conditioning will require a break-in period while operating on straight mineral oil once the engine is back in, so that may be another consideration when releasing the work.
It would certainly be a stretch to include the many possible scenarios associated with different aircraft types and methods used for engine changes. Each aircraft has its own nuances when it comes to installations and rigging procedures and this has been merely a general overview. The engine re-installation process will generally reverse the steps taken for removal only with more care taken to ensure a good clean job. The critical task of installing the engine usually requires a test flight afterwards to ensure that all engine systems are operating properly. This function can be tied to the release of the work in the form of a conditional maintenance release. This action releases the maintenance part of the work with the condition that the aircraft operates as expected. A final sign-off by the pilot essentially completes the release now that both requirements have been satisfied.

The engine represents one of the primary aircraft components that will always be depended upon to provide power for the aircraft and take you where you want to go. It only makes sense to treat it with the respect it deserves. These engines are tough and durable but will provide less than optimum performance if not operated or serviced properly. Do your homework and talk to the pros who have been there and done that. In aviation, we do better when we collaborate between flight operations and maintenance. Many current Club members have had experience with serious engine work and have often sought the advice of other members and Flying Club staff. If you would like to know more about engine work through the Club, please feel free to contact our AMO Maintenance Manager for more information.
Comentarios