Technical dispatch for aircraft renters
- Stuart McAulay
- Mar 1, 2024
- 7 min read
When it comes to renting company aircraft, it’s important to remember that the Brantford Flying Club operates under a Transport Canada approval for our Flight Training Unit (FTU) and other commercial (702/703) aerial services. This means that we have very specific procedures when it comes to the use of club aircraft in order to uphold our commitment to safety and adherence to the Canadian Aviation Regulations (CARs). Even for renters who are not engaged in either of these disciplines, the aircraft must continue to be operated and maintained according to these standards at all times.
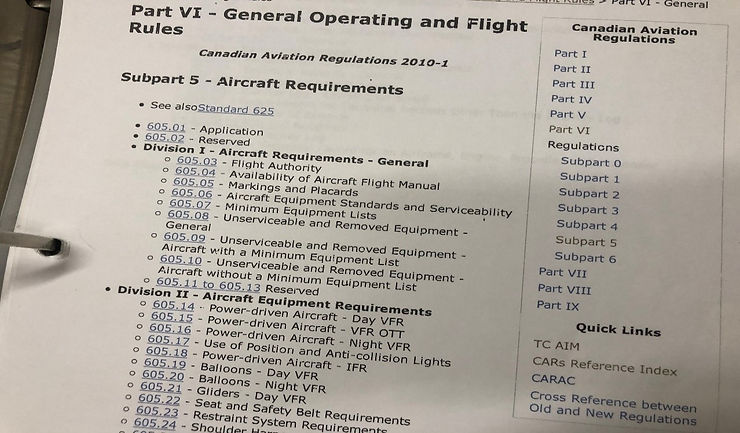
All operators of small aircraft must adhere to the documented requirements found in the Canadian Aviation Regulations. Commercial operators must also have clear procedures indicating how they will continue to meet those requirements on a daily basis.
The primary users of BFC aircraft, such as flight instructors, students, company pilots and renters, are all responsible for doing their part in following company procedures pertaining to the scheduling and maintenance of fleet aircraft. These procedures are all contained within the company Maintenance Control Manual (MCM). As the name suggests, the described procedures are designed to control the actions which must be taken to ensure that scheduled inspections are performed on time and that unscheduled defects are reported and assessed properly. The club is fortunate to have their own aircraft maintenance department which handles all of these requirements as well as providing maintenance and coaching services to private aircraft owners. All commercial aircraft must be maintained by an Approved Maintenance Organization (AMO) rated for the type of aircraft being operated.

All commercial aircraft must be maintained by an Approved Maintenance Organization that is rated for the aircraft types used by the operator. Maintenance staff are trained to evaluate reported defects in order to determine continued airworthiness.
Technical dispatch is the term given to the system used to ensure that aircraft are released (dispatched) only in an airworthy condition. The primary means used to control technical dispatch is through the journey log for each individual aircraft. All entries into the journey log tell the story of that aircraft. This includes flight entries, scheduled maintenance entries, and unscheduled maintenance entries (aka snags or defects). A simple review of the journey log before flight provides the pilot (or anyone) with the actual airworthiness status of the aircraft at any given time. We can determine when the next oil change or inspection is due (or when the previous ones were done), we can see any deferred defects, or whether there are any outstanding defects yet to be addressed by maintenance. This ongoing aircraft story must demonstrate continuity throughout all documented flight and maintenance events according to the regulatory expectations described in our manual.

The aircraft journey log is considered to be the primary means of determining technical dispatch. The journey log provides details on the past, present and future of the aircraft and must be referenced prior to each and every flight.
Each club aircraft also adheres to a specific maintenance schedule which is designed to provide specific manufacturer scheduled requirements as well as those required by the regulations. These events are referred to as out-of-phase items because their inspection cycle does not always coincide with the regular 100 hour inspections. In order to help the pilots review this information, we have added colored sticky tabs on the journey log pages that reference specific events including inspection, oil change, compass calibration, ELT certification, and altimetry certifications. These tabs merely provide a quick reference for items routinely requested by instructors, students and renters of company aircraft.
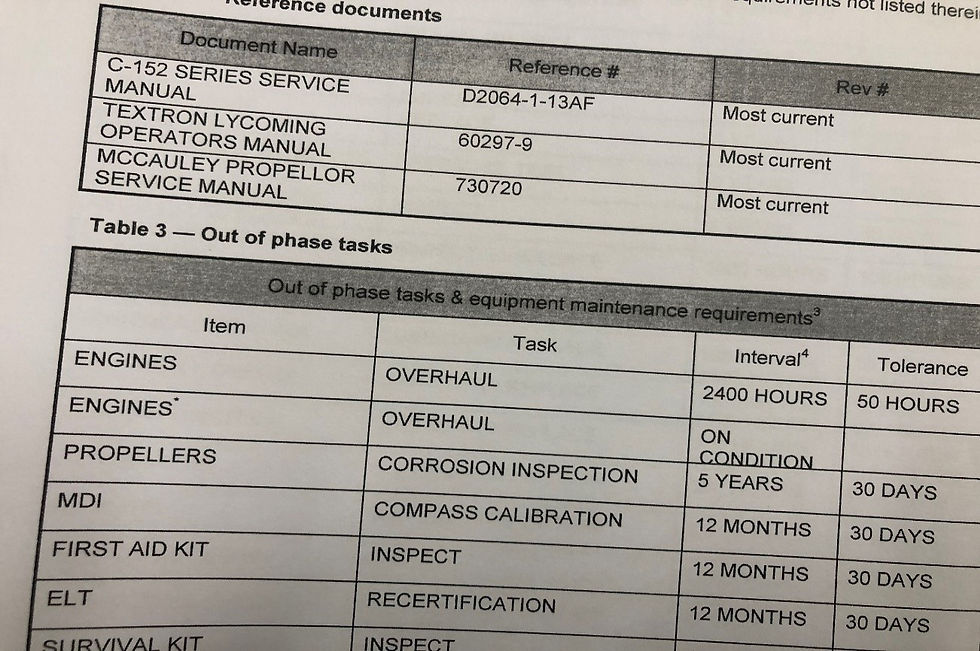
The aircraft maintenance schedule provides details for all scheduled and out-of-phase work applicable to the aircraft. Approved tolerances also factor into the recommended intervals for scheduling purposes and effective maintenance planning.
The typical dispatch process for BFC aircraft starts with the Person Responsible for Maintenance (PRM) and also involves the Service Manager, office staff and all those using the aircraft. The PRM is ultimately responsible to ensure that all maintenance schedule requirements are being met. The Service Manager tracks these items with an electronic tracker and reviews the status of each aircraft daily. The office staff co-ordinate aircraft bookings around maintenance and make the necessary changes when unforeseen events are cause for grounding the aircraft. Any questions regarding the journey log entries must be brought to the attention of the Chief Flight Instructor (CFI), the Assistant CFI, or the Service Manager in order to clarify what is written in the book.
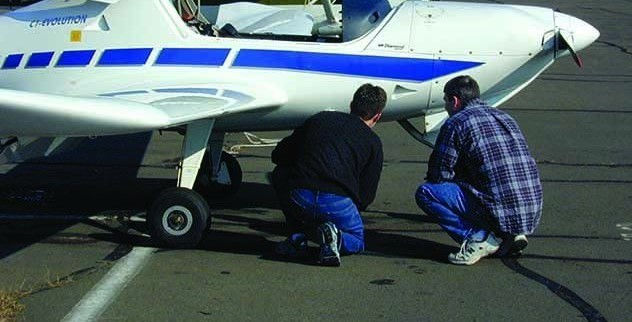
Part of the flight training experience for students is to learn the technical aspects of the aircraft in order to complete an effective pre-flight inspection and spot any potential issues. Flight Instructors and maintenance personnel are both integral to the mentoring process of students as they keep learning.
An often misunderstood concept of technical dispatch seems to be the defect reporting process. It should be a clear process but for some reason there are conflicting opinions about what the book says and what seems to be the most convenient decision in the moment. The need to report a defect is often influenced by scheduling limitations or pressure to complete the intended flight. This should never happen as it only leads to more bad decisions. The manual clearly describes specific actions to be taken when a defect or suspected defect has been identified on the aircraft. A summary of those actions starts with the discovery of a technical concern during the pre-flight, during ground run or in flight, or even on a post-flight inspection. It depends upon the pilot’s ability to recognize a reportable defect - which also comes with experience. A reportable defect is generally defined as any observed condition that could affect the airworthiness of the aircraft. This creates a critical obligation for the pilot-in-command to determine whether the observation is simply noteworthy or whether it could indeed have potential to affect proper operation of the aircraft. This decision obviously requires some knowledge of the aircraft, otherwise the next step should include consultation with a more experienced pilot or an AME whenever possible. I emphasize this consultation step because many of our pilots are students and are just getting to know their way around the aircraft. Without proper consultation, they would be obligated to write every finding into the journey log just to be safe. A meaningful consult with an experienced individual promotes the educational process and can easily disqualify any reports that have no effect on airworthiness thus avoiding unnecessary down time.
With that being said, the pilot is otherwise obligated to make a defect entry whenever these consulting opportunities are not available. Defects which describe obvious damage or malfunction must be entered in the journey log without hesitation. This grounds the aircraft until it can be assessed by maintenance. Remember that a defect entry is merely a description of the problem and not an attempt to include a probable cause. Even though a defect entry in the journey log ultimately grounds the aircraft, we often attach a red warning tag on the throttle control which indicates that the aircraft must not be operated. The warning tag provides an easy visual reference (aka a safety net) to anyone assuming that the aircraft may be serviceable without reference to the log entry. There is a red tag in the glove box of each aircraft to be used for this purpose.
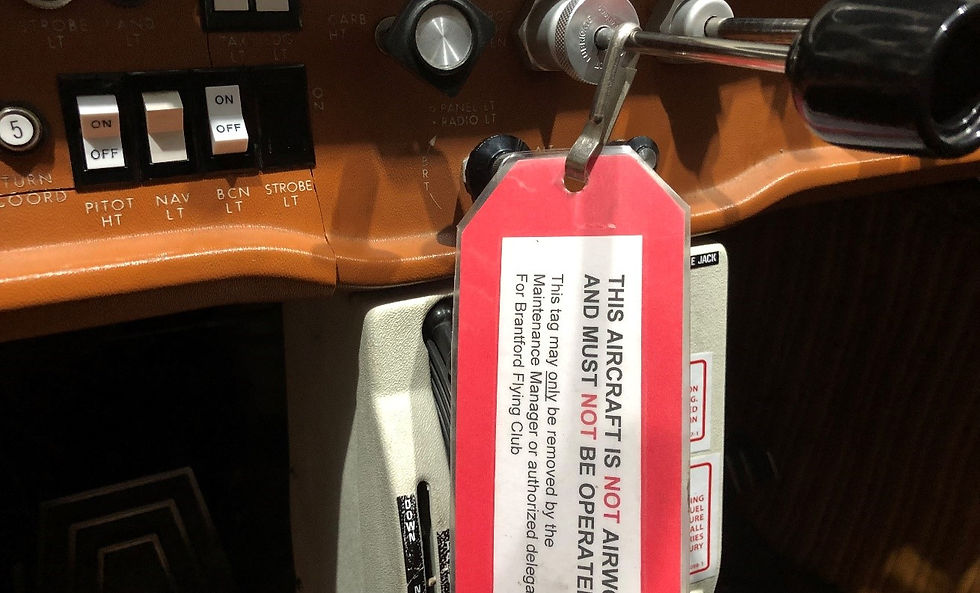
The red unserviceable tag serves as a strong visual indicator that the aircraft has a known or suspected defect. The tag can only be removed by maintenance personnel once they have evaluated the concern and returned the aircraft to service.
It is quite common for club aircraft to be rented after regular business hours or weekends when students/renters may not be able to consult with a company authority concerning a potential defect. In this case, it may be possible to describe the defect via phone call or text with the appropriate person on call otherwise it must be entered into the log book. Whenever a renter is faced with reporting a defect after hours, he/she must complete the reporting process of entering the defect in the journey log, placing the red tag on the throttle control, and then contacting the office to verify that the aircraft is grounded due to a defect.
Keep in mind that, upon discovering a true defect, it is not acceptable to simply cancel the flight and leave the aircraft as it was. Once again, the action of entering the defect is necessary to tell the story of that aircraft. This is the pilot’s responsibility, or person who discovered the defect, to make this happen. A clear description of the defect with sufficient detail is essential to the maintenance crew who will investigate based upon that report. If additional details are available to further describe the defect then a simple phone call or text to the CFI or Service Manager is also acceptable. Calling to provide additional details over the phone does not alleviate the need to actually enter the defect in the log book.
Defects which occur away from base must be reported through phone consultation in order to determine whether there is an actual defect. In some cases, a reported defect may be deferred by the PRM if it does not directly affect the airworthiness of the aircraft. This can also be done over the phone and the pilot would follow up the defect entry with a telephone deferral statement. Certain deferrals may be initiated along with a specific operating restriction depending on the nature of the defect as determined by the PRM or on-call AME.
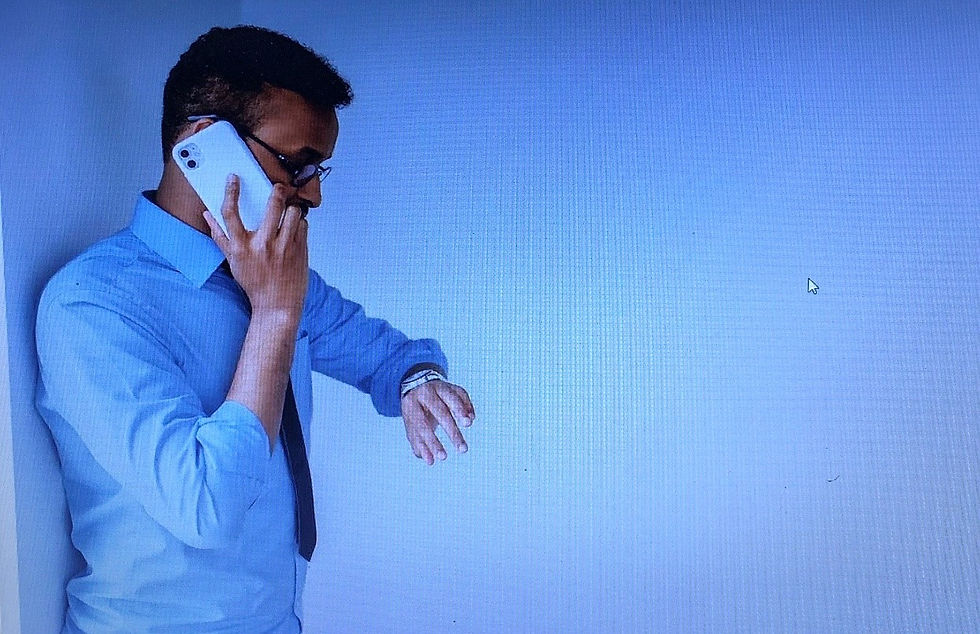
The pilot-in-command is responsible for initiating clear communication with a company authority regarding any defect concerns while away from base. Any deferral confirmed by the Maintenance Manager over the phone must be documented in the journey log before further flight.
Whenever an aircraft has been confirmed with a documented defect and grounded away from base, it must be repaired on-site unless provisions are made for a ferry permit - but this happens only in limited cases. In this situation, the BFC will either contract a local maintenance facility to do the repair provided that they are an appropriately rated AMO or we will send one of our authorized technicians to do the work. So, as you can see from these different scenarios, it is imperative that all operators of BFC aircraft remain aware of the procedures outlined in the manual.
I trust that this information has provided some further insight into understanding how technical dispatch works within a commercial flight operation. The manual always provides a detailed process for aircraft dispatch and how to deal with defects. Please ensure that you review and understand these details and consult with authorized BFC staff whenever possible. Technical dispatch procedures are most effective when we all understand the role we play when using company aircraft.
Comments